【驛站快訊】鋰離子電池在科技界扮演著核心角色,為智慧手機和智慧汽車等各種設備提供動力。日本一位電池開發者表示,他有辦法將鋰電池的量產成本降低90%,與此同時顯著提高其安全性。
曾負責日產汽車(Nissan Motor Co.)電池研究的堀江英明(Hideaki Horie)于2018年成立了總部位於東京的APB公司,以生產“全聚合物電池”。
此前,日產汽車已向APB公司許可了一項先進技術,以生產這種電池。日產汽車于1990年代初開始研發鋰離子電池,於1997年推出了Prairie Joy EV,並成為在商用電動汽車中安裝鋰離子電池的先驅。
今年早些時候,APB公司獲得了包括建築商大林組株式會社(Obayashi Corp.)、工業設備製造商橫河電機株式會社(Yokogawa Electric Corp.)和碳纖維生產商帝人株式會社(Teijin Ltd.)在內的一批日本企業的支援。
今年3月,APB籌集了80億日元(合7400萬美元)(約21.97億新台幣),雖然這筆錢顯得有些微不足道,但足以為一家擬于明年開始量產的工廠提供全套設備。堀江英明估計,其位於日本中部的工廠至2023年裝機容量將達到10億瓦時。
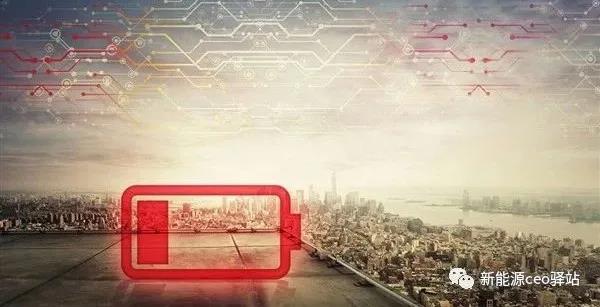
成本更低 容量更大
“現在製造鋰電池的問題在於,它的器件生產類似於半導體,”堀江英明在接受採訪時表示,“我們的目標是使其更像鋼鐵生產。”
電池基本單元——電池芯的製造是一個複雜的過程,需要在潔淨室條件下完成——需要控制濕度、持續的空氣過濾,以防止高反應性材料受到污染。條件如此嚴苛,以至於像韓國的LG化學、中國的寧德時代和日本的松下電器這樣的頂級電池公司需要斥資數十億美元來建造工廠。
堀江英明的創新之處在於用樹脂結構代替電池的基本元件——金屬內襯電極和液態電解質,從而提高了安全性並降低了成本。他說,這種方法大大簡化並加快了生產進程,就像“黃油抹面包”一樣容易。
新型電池單元的正面和背面由聚合物集電器製成,正面和背面分別具有負極性或正極性,並構成電池盒的一部分。10米長的電池片可以“像座墊一樣”堆疊在一起,從而增加容量。
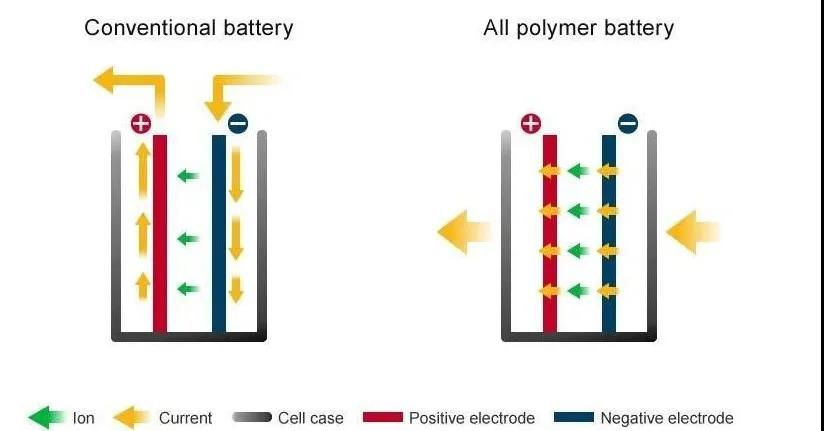
傳統電池和全聚合物電池示意圖
安全性提升
鋰離子電池自近三十年前首次商業化以來已經走過了漫長的道路。與十年前相比,它們的使用壽命更長,功率更大,成本降低了85%,成為推動智慧手機和平板電腦內部功能越來越強大的主力軍。
但是安全性仍然是一個問題,從特斯拉(Tesla Inc.)汽車到波音公司(Boeing Co.)的夢幻客機以及三星電子(Samsung Electronics Co.)的智慧手機,電池一直是引起火災的“罪魁禍首”。
堀江英明說:“從物理學角度來看,鋰離子電池是人類創造的最好的加熱器。”
不過,樹脂電池在被刺破時具有防火性。在傳統電池中,一個刺孔會產生成百上千安培的電湧,是普通家庭電流的好幾倍。溫度會上升到700攝氏度。而APB的電池使用所謂的雙極設計,它消除了目前的電力瓶頸,並允許電池的整個表面吸收電湧,從而避免了這種災難性的情況。
“由於發生了很多事故,安全一直是行業內的頭等大事,”Wood Mackenzie儲能團隊高級分析師Mitalee Gupta表示。“如果該公司能夠迅速擴大規模,這對於存儲和電動汽車應用來說都是一個突破。”
並不完美 聚焦固定電池領域
但是這項技術也不是沒有缺點。總部位於加利福尼亞的諮詢公司Total Battery Consulting Inc.的總裁Menahem Anderman認為,聚合物的導電性不如金屬,這可能會嚴重影響電池的承載能力。
他表示,雙極設計的一個缺點是電池芯在電池中背對背連接,使對單個電池芯的控制變得困難。他還質疑節省下來的費用是否足以與現有企業競爭。“在未來15年或更長時間內,鋰離子液態電解質仍將是主要應用,”他說。
堀江英明承認,APB無法與那些已經投資數十億美元並從規模經濟中受益的電池巨頭競爭。APB不會將目光投向汽車行業的“紅海”,而是將業務重點放在建築、辦公室和發電廠使用的固定電池上。